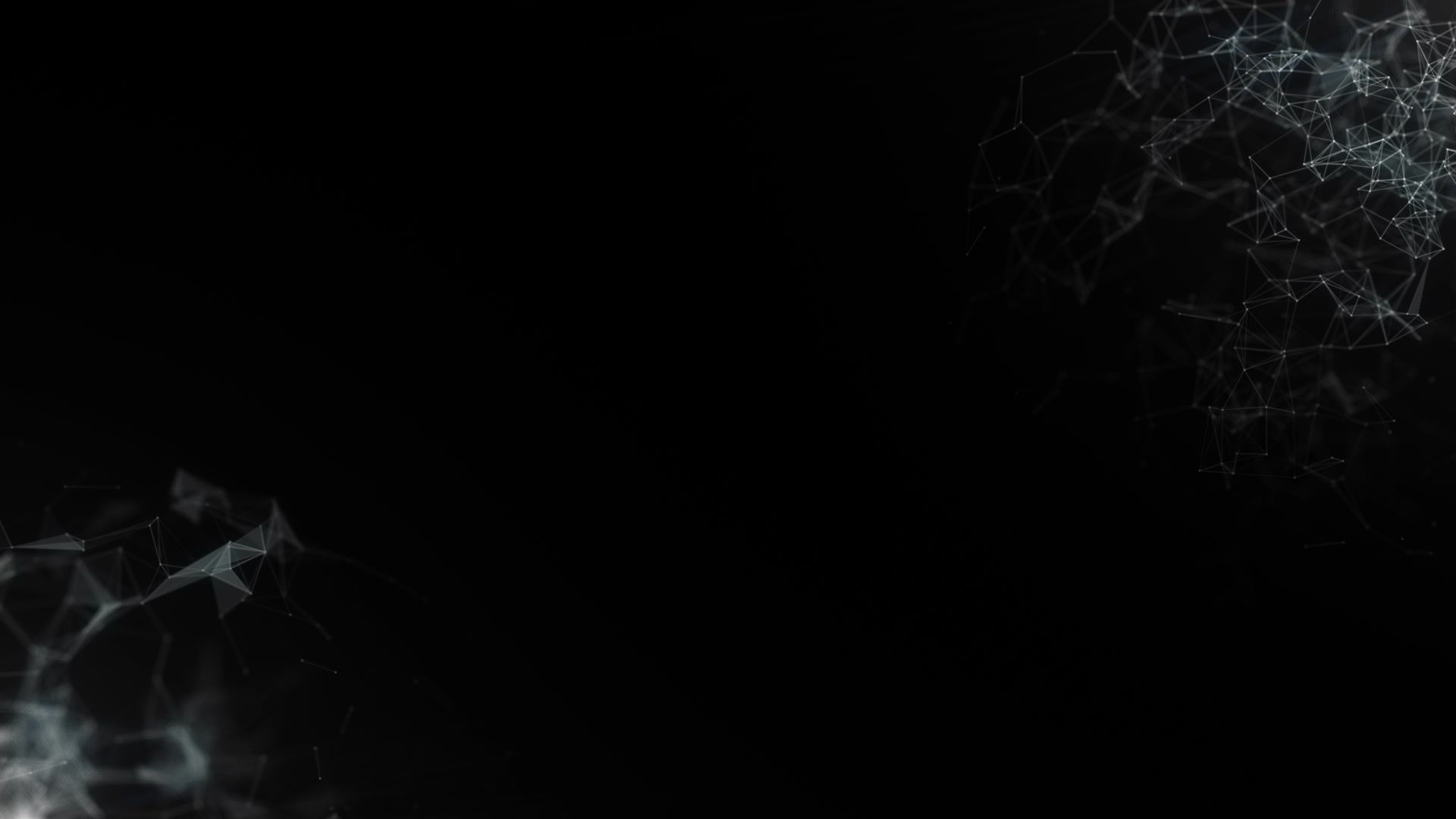
NEXGEN PROCESS:

Quality Consultants for AS9100 & ISO
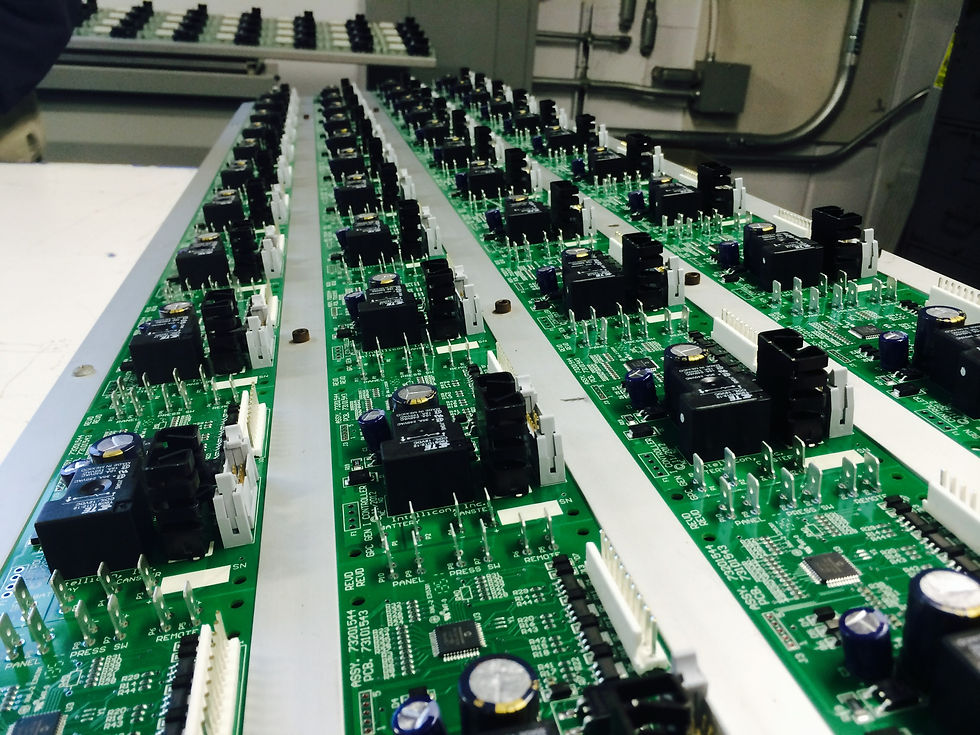
Quality Consultants for AS9100 & ISO
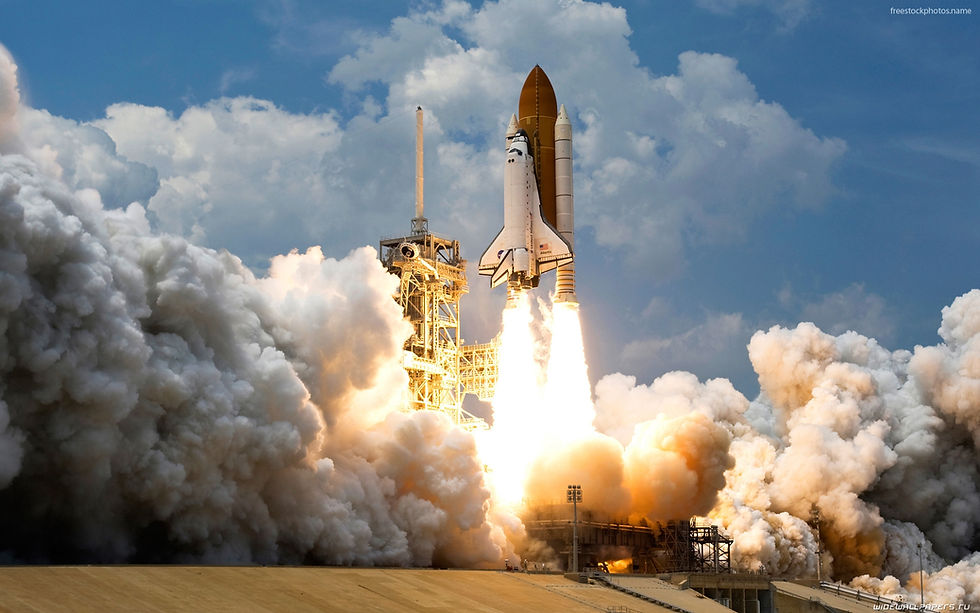
Quality Consultants for AS9100 & ISO

Quality Consultants for AS9100 & ISO

Quality Consultants for AS9100 & ISO
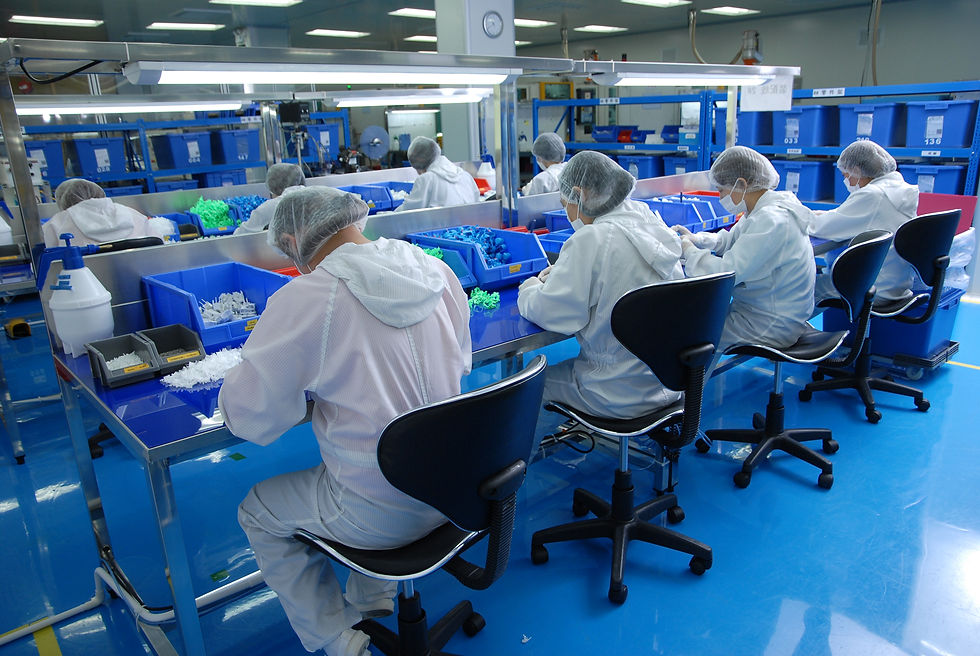
Quality Consultants for AS9100 & ISO
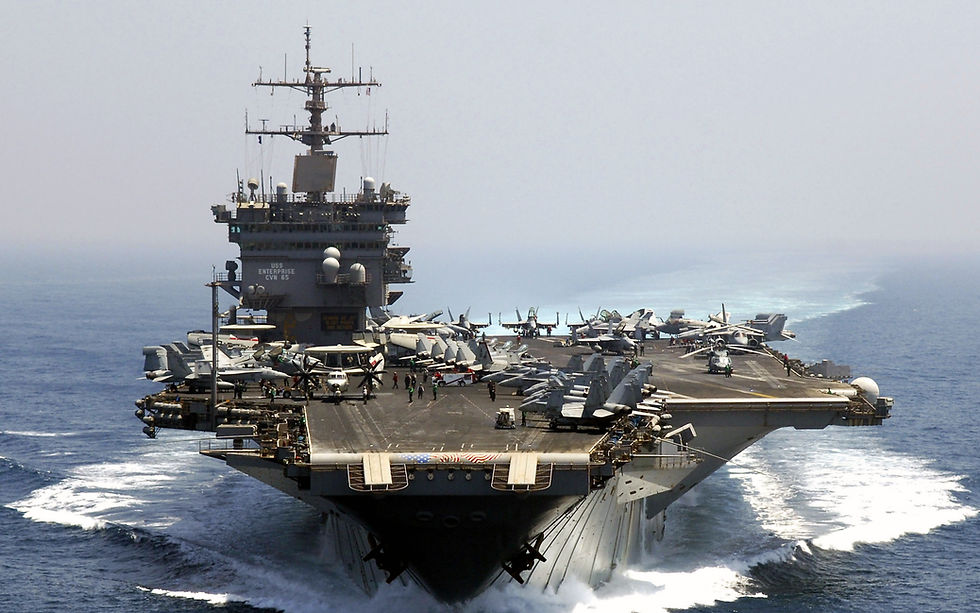
Quality Consultants for AS9100 & ISO

Quality Consultants for AS9100 & ISO
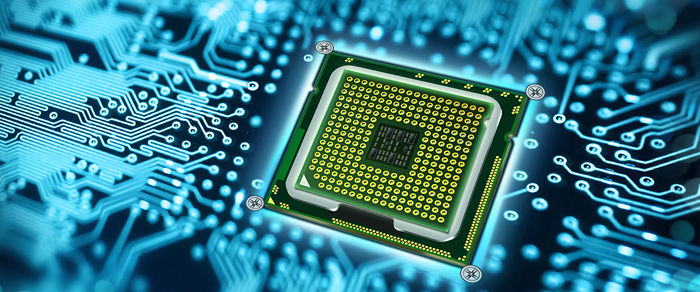
Quality Consultants for AS9100 & ISO
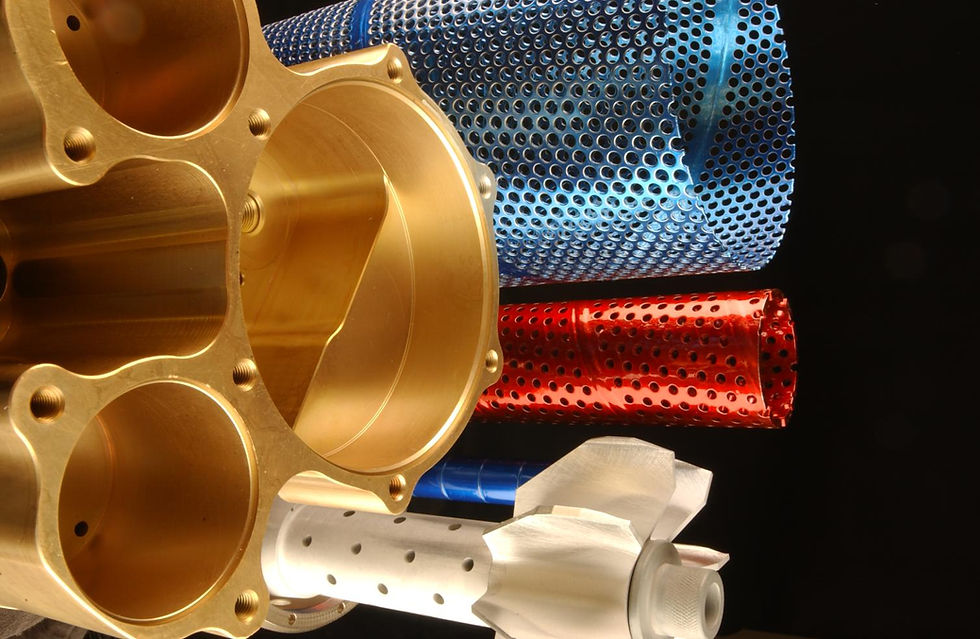
Quality Consultants for AS9100 & ISO

Quality Consultants for AS9100 & ISO
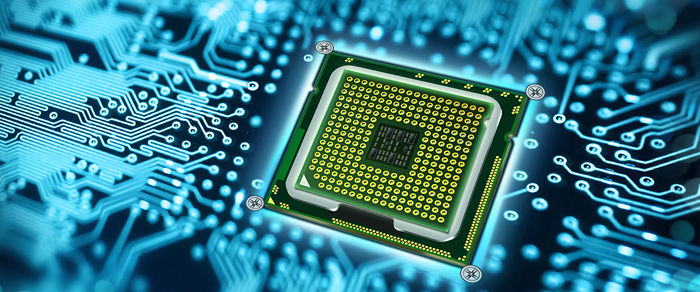
Quality Consultants for AS9100 & ISO

Quality Consultants for AS9100 & ISO

Quality Consultants for AS9100 & ISO

Quality Consultants for AS9100 & ISO

Quality Consultants for AS9100 & ISO
With our custom tailored ISO/AS System. We mold it around your business and company needs, integrating new tools to assist in managing the quality management system without making unnecessary internal changes to your current business practices. Let us show you how easy and convenient it will be. Our expert consultants will be there to guide you through the entire audit.
AT NEXGEN OUR PROCESS STARTS WITH YOUR BASE PROCESSES!

Company Gap Assessment
STEP 1

Process Identification
STEP 2
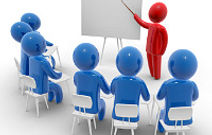
Employee Training
STEP 3

Internal Audit
STEP 4

Maintain The QMS System
STEP 8

Continual Improvement
STEP 7
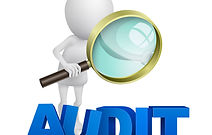
Registration Audit
STEP 6
Management Review

STEP 5
STEPS BROKEN DOWN
-
STEP-1
GAP ASSESSMENT
Nexgen will conduct an on-site visit to your facility meeting with your process owners. During this meeting we will ask the process owner to define their process. We do this to compare your current process to the quality management system requirements. We then will beable to identify the gaps between your process and the quality management system requirements; along with the gaps we will identify the resources (procedures, training, implementation, etc...) to fill these gaps to match the standard.
-
STEP-2
PROCESS IDENTIFICATION / CONTROL / MONITOR / MEASUREMENT
Working with your department managers and process owners; Nexgen will determine the best method to control your processes. We will then identify if procedures are required or recommended, in addition what training will be required to ensure the process is working effectively,efficiently and systematically with your company and its needs. Then determining measurable objectives for each process so that the management team will be able to review current and accurate data to identify if the process is meeting their expectations and copmpany needs/goals.
-
STEP-3
EMPLOYEE TRAINING
Nexgen will generate a training matrix and training plan to be implemented by your company. Based on the process controls employees will need to be introduced and/or made aware of the control mechanisms implemented around the processes they will be working wiothin. In addition each employee will need some basic information about ISO 9001 and their role in assisting the company in achieving,maintaining and continually improving the ISO 9001 Quality Management System for your company.
-
STEP-4
INTERNAL AUDIT
Once the training has been completed and the processes controlled. The company will need to begin generated quality records to support the required processes. Nexgen will then conduct a detailed internal audit to determine if the Quality Management System is operating as planned. We will conduct the internal audit in the same manner as a Registration body would conduct their registration audit. This allows the employees to become familiar with the audit process and to get used to answering question related to their process and measurable objectives they will encounture durring an actual audit. The internal audit is complete with a detailed report, checklist and audit findings that are provided to the management team so that they can drive the continual improvement process.
-
STEP-5
MANAGEMENT REVIEW
The AS and ISO standards require that the organization conduct periodic internal management review meetings. During this meeting the management team will review data from their quality management system to determine if the system is effective or where the gaps in the system still are. Nexgen will conduct the first meeting to allow the management team to become familiar with the process and the agenda items.
-
STEP-6
REGISTRATION AUDIT
Know that all the internal ISO requirements have been addressed, implemented, audited and reviewed, it is time for the company to be audited by an outside certifacation body. Nexgen will attend the audit as a supporting function to the company. Once the audit is complete the company will be recommended for certification and the audit results will be reviewed by a review board once approved the company will receive their ISO certification thru the mail and at that time the company can publish the fact that they have achieved ISO certification.
-
STEP-7 & 8
MAINTENANCE & CONTINUAL IMPROVEMENT
Getting ISO certified is often the easy part. Maintaining the system and continual improving the system is sometime the part that seems to fall apart for some companies. If the system is set up correctly during the initial phases of implementation,the maintenance should be part of the day-to-day activities for the company. We always recomend top bring on or internally tyrain a QA Manager to manage the system. If the system is set up to basically pass the registration audit and not to be used for improvement than the system seems to become dormant once the registration audit is complete. It is important that the management team focuses on the corrective and preventive action system along with the internal auditand management review processes. These processes are one of the most important improvement tools within the AS / ISO Quality Management Systems.